Chemical Hygiene Plan
The College of Engineering Chemical Hygiene Plan can be downloaded as a pdf or viewed on the webpage below.
The California State University Long Beach (CSULB) College of Engineering (COE) Chemical Hygiene Plan (CHP) has been designed to fulfill the Cal/OSHA requirement regarding "Occupational Exposure to Hazardous Chemicals in Laboratories," California Code of Regulations (CCR), Title 8, General Industry Safety Orders, Section 5191. The contents of this regulation and its appendices are available to employees at the COE Safety Office, ECS-620. These regulations mandate that where hazardous chemicals are used in the workplace, the employer shall develop and carry out the provisions of a written CHP which is:
- Capable of protecting employees from the health hazards associated with hazardous chemicals present in the workplace
- Capable of keeping exposures below Cal/OSHA-regulated limits
- Readily accessible to employees via hard-copy at the COE Safety Office in ESC-620 and electronically on the COE website
- Reviewed annually and updated, as appropriate.
This CHP, along with the following documents, constitutes the foundation of our employee Health and Safety Program.
- General Safety Awareness Training
- Lab Specific Safety Training
- COE Safety Website
- Campus Injury and Illness Protection Program (IIPP) (pdf)
- Campus Environmental Compliance
- CSULB Emergency Operations Plan (pdf)
- CSULB Environmental Health and Safety Procedures
Student health and safety are also covered by these policies and procedures where applicable. The information presented in the CHP represents best practices and provides a broad overview of the information necessary for the safe operation of laboratories that utilize potentially hazardous chemicals. It is not intended to be all inclusive.
1.1 COE Telephone Contact Information
FOR EMERGENCIES: DIAL 911 from a campus phone.
Office/Person | Phone Number |
---|---|
CSULB Public Safety | 562.985.4101 |
Administrator in Charge, Tracy Maples | 562.985.5123 |
Dean's Office | 562.985.5123 |
Associate Dean for Research, Hamid Rahai | 562.985.8032 |
Associate Dean for Academic Programs, Antonella Sciortino (Acting) | 562.985.8032 |
COE Chemical Hygiene Officer (CHO), Chibuzo Obiefuna | 562.985.4544 |
COE Facilities Coordinator, Glen Seymour | 562.985.8746 |
Biomedical Engineering Department Office | 562.985.2849 |
BME Chair, Shadnaz Asgari | 562.985.8023 |
Chemical Engineering Department Office | 562.985.4882 |
ChE Chair, Roger Lo | 562.985.1508 |
Civil & Construction Engineering Management Department Office | 562.985.5118 |
CECEM Chair, Lisa Star (Acting) | 562.985.5118 |
Computer Engineering & Computer Science Department Office | 562.985.4285 |
CECS Chair, Mehrdad Aliasgari | 562.985.7987 |
Electrical Engineering Department Office | 562.985.5102 |
EE Chair, Henry Yeh | 562.985.4899 |
Mechanical & Aerospace Engineering Department Office | 562.985.1563 |
MAE Chair, Jalal Torabzadeh | 562.985.8181 |
Environmental Health and Safety | 562.985.2283 |
1.2 Designation of Personnel Responsible for Implementation of the CHP
COE will employ a full-time Chemical Hygiene Officer (CHO), responsible for implementation of the Chemical Hygiene Plan (CHP) and management of the Environmental, Health & Safety (EH&S) Program in the COE.
1.3 Annual Review of CHP
The CHP will be reviewed annually as required under 8 CCR 5191(e)(4). A copy of the change log can be found in Section 14.
The scope of this CHP includes all students, faculty, and staff working with hazardous material in laboratories and on projects in the ollowing areas:
- Engineering Technology (ET), Engineering 2 (EN2), Engineering 3 (EN3), Engineering 4 (EN4), Engineering & Computer Science (ECS), and Vivian Engineering Center (VEC); and
- Antelope Valley Engineering Program.
Action Level—used by OSHA and NIOSH to express a health or physical hazard. They indicate the level of a harmful or toxic substance/activity which requires medical surveillance, increased industrial hygiene monitoring, or biological monitoring.
Administrative Controls—also known as work practice controls which are changes in work procedures such as written safety policies, rules, supervision, schedules, and training with the goal of reducing the duration, frequency, and severity of exposure to hazardous chemicals or situations.
Biohazardous Waste—also called infectious waste (such as blood, body fluids, and human cell lines), is waste contaminated with potentially infectious agents or other materials that are deemed a threat to public health or the environment.
Cal/OSHA—California Division of Occupational Safety and Health. Regulatory agency charged with setting and enforcing standards, providing outreach and issuing permits.
Carcinogen—any substance, radionuclide or radiation that promotes carcinogenesis, the formation of cancer.
CCR Title 8—California Code of Regulations Title 8. Regulations pertaining to workplace safety.
Chemical Hygiene Officer (CHO)—responsible for ensuring implementation of CHP.
Chemical Hygiene Plan (CHP)—a document required under California regulations 8 CCR 5191 for facilities that have laboratories that utilize hazardous materials.
College of Engineering (COE)—one of the Colleges at California State University Long Beach (CSULB).
Corrosive—U.S. DOT hazard classification; a chemical that produces destruction of skin tissue, namely, visible necrosis through the epidermis and into the dermis, in at least 1 of 3 tested animals after exposure up to a 4-hour duration.
DEA—Drug Enforcement Administration. Federal agency charged with enforcement of the controlled substances laws and regulations of the United States.
DOT—United States Department of Transportation
EH&S—Environmental Health and Safety Campus Department. Involved in environmental protection, safety at work, occupational health and safety, compliance and best practices.
Engineering Controls—strategies designed to protect workers from hazardous conditions by placing a barrier between the worker and the hazard or by removing a hazardous substance through air ventilation.
EPA—United States Environmental Protection Agency
Flammable—DOT hazard classification; usually pertaining to liquids with flash point of 140° F or less.
GHS—Globally Harmonized System of classification and labelling of chemicals. GHS defines and classifies the hazards of chemical products and communicates health and safety information on labels and safety data sheets.
Hazardous Materials—any item or agent (biological, chemical, radiological, and/or physical), which has the potential to cause harm to humans, animals, or the environment, either by itself or through interaction with other factors.
Hazardous Waste—a waste with properties that make it potentially dangerous or harmful to human health or the environment. It can be in the form of liquid, solid or contained gases and typically highly regulated. It must be collected and handled per strict campus guidelines.
HAZCOM—CSULB campus Hazard Communication Program.
Injury and Illness Prevention Program (IIPP)—campus-wide safety program which details the means and methods CSULB uses to ensure the safety and health of its employees.
Laboratory Supervisor—used synonymously with Principle Investigator (PI) who is in charge of laboratory operations. Can also be a designated supervisor such as a post-doc working under a PI.
Local Exhaust Ventilation—a type of engineering control to reduce exposures to airborne contaminants such as dust, mist, fume, vapor or gas in the workplace. Simply put it is something that sucks an airborne contaminant out of the workplace.
Mutagen—an agent such as radiation or a chemical substance, that causes genetic mutation.
“Near-miss” Incident—a narrowly avoided collision, accident, or incident which is used to foretell future EHS concerns
National Institute for Occupational Safety and Health (NIOSH)—United States federal agency responsible for conducting research and making recommendations for the prevention of work-related injury and illness. Part of the Centers for Disease Control and Prevention, within the U.S. Department of Health and Human Services.
Oxidizer—DOT hazard classification for chemicals that can yield oxygen and thus enhance the combustion of other materials.
National Institute for Occupational Safety and Health (NIOSH) Permissible Exposure Level (PEL) —a legal limit in the United States for exposure of an employee to a chemical substance or physical agent. For chemicals, the PEL may be expressed in parts per million (ppm) or milligrams per cubic meter (mg/m3). (Note: see Table AC-1 at https://www.dir.ca.gov/title8/5155table_ac1.html for chemical contaminants.)
Particularly Hazardous Substance (PHS) — dangerous chemicals that are known to have immediate or long-term toxic health effects. Divided into three primary groups; Acute Toxins, Reproductive Toxins, and Carcinogens.
Principal Investigator (PI)—usually a professor in charge of a laboratory or set of laboratories who is actively undertaking research. They are considered the front-line supervisor and are responsible for training and personnel safety in the laboratory.
Poison—DOT hazard classification for materials that are a liquid with a LD50 (Lethal Dose of 50%) oral of not more than 500 mg/Kg, or a solid with an LD50 oral not more than 200 mg/Kg, or a compound with a LD50dermal not more than 1000 mg/Kg, or a dust/mist with a LD50 or not more than 10 mg/L.
Personal Protective Equipment (PPE)—Protective clothing, hard hat, face shield, goggles, safety glasses, safety shoes, gloves or other garments or equipment designed to protect a worker from injury exposure or infection.
PPFM—Physical Plant and Facilities Management.
Safety Data Sheets (SDS)— informational literature required by the GHS System for hazardous materials and intended to provide comprehensive information about a substance or mixture for use in chemical management and safety.
Sharps Container—Hard plastic container that is used to safely dispose of hypodermic needles and other sharp medical instruments, such as an IV catheters and disposable scalpels.
Standard Operating Procedure (SOP)—a written set of instructions that document how to safely perform work involving hazardous chemicals or hazardous operations. Includes training documentation.
Teratogen—an agent or factor which causes malformation of an embryo.
Responsibilities of COE Administrators
The responsibilities of Administrators are to ensure the following:
- COE EH&S safety programs are implemented and conducted where required.
- Adequate guidance and support are provided to Departments and PIs to ensure programs implementation.
- Periodic review of the EHS goals and metrics to ensure successful program implementation.
4.2Responsibilities of Principal Investigator (PI)/Laboratory Supervisor
You are a Laboratory Supervisor if you direct or oversee the work of any students (class or lab work, student research projects, thesis work) and/or student employees, including Teaching Assistants, Graduate Assistants, Research Assistants/Associates, Student Assistants, College Work Study Students, or volunteer workers.
The PI/Laboratory Supervisor has responsibility for the health and safety of all personnel working in his or her laboratory who handle hazardous chemicals. The PI/Laboratory Supervisor may delegate safety duties but remains responsible for ensuring that delegated safety duties are adequately performed. The PI/Laboratory Supervisor is responsible for:
- Knowing all applicable health and safety rules and regulations, training and reporting requirements, and standard operating procedures associated with chemical safety for hazardous materials and hazardous wastes used or generated under their direction.
- Identifying hazardous conditions or operations in the laboratory, determining safe procedures, and implementation and enforcement of those procedures.
- Establishing SOPs (general and protocol specific) and performing literature searches relevant to health and safety for laboratory-specific work. Use template in Appendix E.
- Ensuring all people working in your lab have completed the COE General Safety Awareness Training and have taken the safety quiz prior to beginning work.
- Obtaining prior approval for the use of hazardous chemicals from the CHO.
- Prior to starting work ensuring a “Project Safety Review and Authorization” form is approved for all project work conducted outside of regularly scheduled classroom/laboratories.
- Monitoring all work practices in lab to ensure safety rules are followed.
- Maintaining an updated chemical inventory for the laboratory using RSS system. All hazardous chemicals (as defined in CCR Title 8 §5191 or as stated on the Safety Data Sheet) are to be entered into the inventory system when received and removed after disposal.
- Ensuring laboratory or other personnel under his/her supervision have access to and are familiar with the appropriate SDSs, SOPs, and safety manual.
- Training all laboratory or other personnel supervised to work safely with hazardous chemicals.
- Providing documented training records of laboratory-specific or specialized training to CHO prior to start of work or at the beginning of each semester for classes requiring training.
- Promptly notifying CHO should engineering controls (e.g., fume hoods) or safety equipment (e.g., emergency showers/eyewashes, fire extinguishers, etc.) become non-operational.
- Ensuring availability of all appropriate personal protective equipment (PPE) (e.g., laboratory coats, gloves, eye protection, etc.) and that available PPE is maintained in working order;
- Conducting periodic self-inspections of laboratory
- Promptly reporting accidents and injuries to COE CHO, Administrative Services Manager and/or the Worker’s Compensation Manager. Serious injuries MUST be reported to the Worker’s Compensation Manager immediately to allow for compliance with the CAL/OSHA 8-hour reporting time frame. Any doubt as to whether an injury is serious should favor reporting. See contact list on page 5.
- Working with the CHO ensure medical surveillance, consultation and/or examination is conducted for personnel that may have been exposed to a hazardous chemical. COE to provide funding. When possible establish engineering controls (e.g. fume hood, gloves, etc..) to eliminate the potential for exposure.
- Informing facilities personnel, non-laboratory personnel, and any outside contractors of potential laboratory-related hazards when they are required to work in the laboratory environment.
- Identifying and minimizing potential hazards to provide a safe environment for after-hours repairs and renovations.
- Ensuring that chemicals and supplies in the laboratory area are maintained in an orderly manner to reduce the risk of contamination or exposure and reduce risk of trip hazards.
- Ensuring laboratory security, including management of key distribution to authorized personnel (see Section 13).
4.3 Responsibilities of Personnel (Employees and Students) Who Handle Hazardous Chemicals
Personnel in research or teaching laboratories who use, handle, or store potentially hazardous chemicals are responsible for:
- Completing required training for the lab prior to starting work.
- Following verbal and written laboratory safety rules, regulations, and standard operating procedures required for the tasks assigned.
- Developing good personal chemical hygiene habits, including but not limited to, keeping the work areas safe and organized.
- Planning, reviewing and understanding the hazards of materials and processes prior to conducting work.
- Utilizing appropriate measures to control identified hazards including consistent and proper use of engineering controls, personal protective equipment, and administrative controls.
- Understanding the capabilities and limitations of PPE.
- Gaining prior approval from the PI/Laboratory Supervisor for the use of restricted chemicals and materials.
- Consulting with the PI/Laboratory Supervisor before using particularly hazardous substances (PHS) or conducting certain higher-risk experimental procedures.
- Properly storing, handling, labeling and disposing of hazardous waste.
- Immediately reporting all accidents and unsafe conditions to the PI/Laboratory Supervisor.
- Completing all required health, safety and environmental training and providing written documentation to their supervisor.
- Informing the PI/Laboratory Supervisor of any work modifications ordered by a physician as a result of medical surveillance, occupational injury, or exposure.
- Ensuring laboratory security by preventing unauthorized access (see Section 13.0).
- When working autonomously or performing independent research or work:
a. Reviewing the plan or scope of work for their proposed research with the PI/Laboratory Supervisor.
b. Notifying in writing and consulting with the PI/Laboratory Supervisor, in advance, if they intend to significantly deviate from previously reviewed procedures (Note: Significant change may include, but is not limited to, change in the objectives, change in PI, change in the duration, quantity, frequency, temperature or location, increase or change in PPE, and reduction or elimination of engineering controls.)
c. Preparing Standard Operating Procedures (SOPs) and performing literature searches relevant to safety and health that are appropriate for their work.
d. Providing appropriate oversight, training and safety information to laboratory or other personnel they supervise or direct.
- Understanding and complying with all safety guidelines, regulations, and procedures required for the task assigned and for reporting unsafe conditions, accidents or near misses to the Principal Investigator, immediate laboratory management staff or COE CHO.
4.4Responsibilities of the Chemical Hygiene Officer (CHO)
The COE CHO has primary responsibility for ensuring the implementation of all components of the CHP including, but not limited to:
- Informing PIs/Laboratory Supervisors of all health and safety requirements and assisting with the selection of appropriate safety controls, personal protective equipment, engineering controls, and training.
- Conducting periodic inspections per IIPP (minimum 10 per calendar year) with laboratory PIs/Laboratory Supervisors and immediately taking steps to abate hazards that may pose a risk to life or safety upon discovery of such hazards.
- Documenting findings from IIPP inspections and tracking thru implementation. Maintain tracking list to report out to administration number of open findings and duration to close.
- Performing hazard assessments as necessary or upon request. Work with PI/Laboratory Supervisors to develop and implement appropriate chemical hygiene policies and practices that satisfy requirements in an efficient manner.
- Having working knowledge of current health and safety rules and regulations, training, reporting requirements and SOPs associated with regulated substances. Such knowledge may be supplemented and developed through research and training materials.
- Conducting safety review and evaluation of COE hazardous materials procurement requests.
- Performing inspection and testing of each COE fume hood at least once annually.
- Providing coordination between COE hazardous waste generators and CSULB EHS to ensure all generated hazardous wastes are properly contained, appropriately labeled, and stored in accordance with campus and regulatory requirements.
- Providing technical guidance and investigation, as appropriate, for all accidents and injuries.
- Reviewing plans for installation of engineering controls and new facility construction/renovation, as requested.
- Reviewing and evaluating the effectiveness of the CHP at least annually and updating it as appropriate.
- Working with Campus EHS to develop or alter programs and policies as laws and regulations evolve.
- Submitting work orders to repair/replace non-operational engineering controls (e.g., fume hoods) or safety equipment (e.g., emergency showers/eyewashes, fire extinguishers, etc.).
- Inspecting all COE fire extinguishers monthly and submit service request to replace/repair as needed.
- Conducting or arranging air, personal, or other industrial hygiene monitoring, as necessary, to ensure safe laboratory exposures.
- Reviewing Project Authorizations as needed or every three years.
4.5Responsibilities of COE Facilities
- Coordinating with COE CHO to review proposed laboratory operational process changes that involve hazardous materials.
- Working with CHO to identify current operations and devices that either utilize a hazardous material or are potentially harmful to employees or students.
- Implementing facility related improvement identified during IIPP inspections.
- Ensuring contractors are familiar with COE safety requirements when starting a project.
[Note: EH&S/DSC is to be notified when contractors perform building structural modifications.]
COE has developed key policies and procedures surrounding present and future research and laboratory operations that utilize hazardous materials. The goal is to ensure safe and sound engineering solutions, operational practices, personal protective equipment and appropriate training are implemented to reduce potential safety and environmental risk to employees, students, contractors, visitors, and the environment.
5.1 COE Safety Policy
All members of the COE community are expected to be thoroughly familiar with their safety responsibilities, strive to follow safety practices at all times, act proactively to prevent accidents and injuries, communicate hazards to supervisors, and be prepared for emergencies that may occur in the workplace.
5.2 Project Review and Authorization Requirement
A Project Review and Authorization approval process is required to ensure COE faculty and staff projects meet COE and EH&S guidelines. This approval process ensures COE activities are conducted in compliance with local, state, and federal regulations.
COE requires the form in Appendix D to be completed for:
- Startup of a new lab for a new faculty member
- A project that generates hazardous waste, involves PHS, or involves specifically regulated activities listed on the project review form
- A project that requires new equipment purchases (CHO will identify which project purchases require pre-approval
- A project that involves a new process which has not been previously approved in COE.
When completing the Project Review and Authorization form please note the following items.
1. Chemicals: List the types of hazardous chemicals used in the project, including significant amounts of hazardous consumer products (gasoline, coatings, adhesives, resins). You may list chemicals by general type/class, but please list key “Extremely Hazardous” chemicals and all Cal/OSHA Regulated Carcinogens.
2. Physical Hazards: List hazardous equipment/operations associated with the project including: motor vehicle travel, climbing, open flames, U.V. light, hazardous lasers, high voltages, microwaves, radiation, plasmas, cryogenics, high pressures, dangerous animals, tools, centrifuges, autoclaves, etc.
3. Biological Hazards: List any pathogenic organisms involved in a project. State if you intend to work with human tissues, blood or blood components.
4. Training Plan: Describe methods you will use to provide documented safety training related to the materials and methods employed in this project. The CHO can support the development of safety training material.
5. Safety Procedures, Equipment, etc.: Briefly describe safety procedures and equipment that will be employed to protect personnel from the hazards. If necessary, refer to the COE CHO for guidance in these areas. Required use of fume hoods, protective clothing, spill prevention/control equipment, fire extinguishers, flammables cabinets, etc. are examples of protective equipment. A mandatory buddy system policy and requiring drivers to obtain a CSULB Defensive Driver's Certificate are examples of safety procedures.
6. Outreach Activities: Demonstrations during such events will put you in contact with the public and often minors. An extra level of safety must be introduced into such activities. Specific approval for each such project is required – and other forms/approvals must be obtained in advance. Contact COE CHO for details.
7. Hazardous Waste: Please indicate if this project will generate hazardous waste, e.g. chemicals, oil, batteries, sharps, etc.
Approval is granted only if appropriate SOPs, engineering controls, monitoring equipment, training and emergency procedures are in place. Other requirements deemed appropriate by COE CHO must also be met. In some instances, department chair, campus EH&S and/or Dean approval are required.
5.3Prior Approval of Laboratory Activities Requirement
Anyone who plans to use strictly regulated or hazardous chemicals (see Section 8.1) or conduct non-standard hazardous activities must obtain prior approval from COE CHO before starting work. Materials which are extremely hazardous, reactive, require special monitoring equipment, or used in such a way that could subject the user to unhealthful levels of exposure would trigger this requirement. Examples include, but are not limited to, the use of hydrofluoric acid, inhalation hazard gases, black powder, and perchloric acid.
Approval is granted only if appropriate SOPs, engineering controls, monitoring equipment, training and emergency procedures are in place. Other requirements deemed appropriate by COE CHO must also be met. In some instances, department chair, campus EH&S, and/or Dean approval are required.
5.4 Measures to Reduce Hazardous Materials Exposure
Use of any hazardous chemical in COE laboratories requires:
1. An assessment as to whether chemical elimination or substitution if feasible
2. Development of appropriate engineering controls
3. Development of Safe-Work Practices
4. Development of administrative controls; and
5. Identification of any required PPE.
Consideration of chemical types and potential exposure routes must be considered. SDSs shall be maintained by each laboratory supervisor and be readily available to all laboratory personnel. Engineering controls specified in SDSs and SOPs will be used to control level of exposure to the chemical in use. Examples of these engineering controls include, but are not limited to, chemical fume hoods, glove boxes, physical shields or barriers, local exhaust ventilation and biological safety cabinets. All chemicals that generate hazardous fumes, mists, or vapors shall be handled inside a properly functioning fume hood or other process enclosure.
Voluntary use of dusk masks and respirators requires users to read and understand California Regulation 8 CCR 5144, Appendix D. The COE CHO shall document that a user had reviewed and understood Appendix D by having the voluntary user sign a form stating user acceptance of the conditions stated in Appendix D.
Laboratory personnel generally do not use personal respirators. Where the use of respirators is necessary to maintain exposure below permissible exposure limits (PELs), the COE CHO will evaluate and if deemed required, will then provide a respirator and the appropriate training to the individual. Respirators will be selected and used in accordance with the requirements of CCR Title 8, Section 5144.
The following criteria will be used when determining any required control measures to reduce an employee’s occupational exposure:
1. Verbal information obtained from employees regarding chemical usage
2. Visual observations of chemical use or laboratory operations
3. Evaluation of existing engineering control measures or administrative practices
4. Any PI/Laboratory Supervisor, CHO, EH&S, and SDS recommendations
5. Cal/OSHA regulatory requirements
6. Recommendations from professional industrial hygiene organizations such as AIHA
7. Direct reading instrumentation results
8. Employee exposure monitoring results
9. Medical evaluation, examination and/or surveillance findings.
Particular attention will be given to the selection of safety control measures for chemicals that are known to be extremely hazardous (See section 8.4).
5.5 Safety Rules in Laboratories
The following safety rules need to be followed when working in a COE laboratory:
1. LOCK UP! If YOU unlocked a room, never leave it unattended. If you leave a room that you unlocked, you could be held responsible if someone gets in and hurts themselves, steals, or damages items in that room in your absence. Nearly every room has expensive items and dangerous chemicals. ALWAYS LOCK UP WHEN YOU LEAVE!
2. No food or drink are allowed in labs. Smoking is not permitted at CSULB.
3. Follow safety instructions or warnings given by people who use the space. If instructed to exit the premises, please do so.
4. Do not enter a room posted on the outside with a temporary sign stating, "KEEP OUT," "DANGER," or equivalent wording. Room conditions inside may be dangerous or sensitive requiring others to stay out for a period of time. The CHO and/or EH&S shall be notified of such conditions prior to posting. Contact the CHO or laboratory personnel for updated conditions.
5. When entering areas containing hazardous chemicals or hazardous equipment do not touch items on laboratory benches or in fume hoods. DO NOT PUT ANY TOOLS OR OTHER ITEMS ON LABORATORY BENCHES OR SINK AREAS THAT ARE MARKED WITH WARNING LABELS.
6. If equipment or chemicals are in the way of conducting a work task, ask either the PI/Lab Supervisor, or their designated person, to move them to a safe location. Do not move the chemicals yourself.
7. Always read warning signs and labels on items in the rooms, such as "Danger - High Voltage," "Corrosive," "Poison," "Flammable," "Oxidizer," etc. Do not touch these items and use extreme caution when working in the room.
8. Always read signs placed on trash cans in the rooms. Plastic, cardboard, and metal trash cans or baskets are sometimes used for special purposes. For example, some containers are used for the collection of broken glass. DON’T TOUCH containers used for the collection of biohazardous/Medical Waste (containers with RED bags and “Biohazard” labels).
NEVER THROW BROKEN GLASS OR SHARP ITEMS IN THE REGULAR TRASH. Use specially labeled boxes that are used to collect broken laboratory glass, etc., and are found in most labs. For custodians, if you see sharp items in the trash, do not touch them; leave them there and notify your supervisor.
9. Note the locations of eyewash/shower units as you enter the laboratories and observe how they work. Once turned on, they must be turned off by hand; turn off is NOT automatic. Knowing how they work can prevent a flood if a falling object accidentally turns one on. [DOWN = ON. UP = OFF].
Use this equipment if you get chemicals on your body or in your eyes, either from accidents involving laboratory chemicals or from service chemicals such as corrosive cleaners, strippers, solvents, battery acid, etc. To use the shower or eyewash, turn it on and flush a contaminated body part for 15 minutes. The floor will flood as most units have no drains. Your health is the most important thing.
Areas beneath eyewash/shower units MUST remain clear of boxes, trash cans, equipment or other items at all times. Do not place any items beneath eyewash/shower units that would block access during an emergency. Report any blocked units to your supervisor or the COE CHO.
10. NEVER clean up or touch a puddle of liquid unless it is OBVIOUSLY from a water leak (it could be acid or a poisonous chemical). Report suspicious spills to your supervisor.
11. Always check for natural gas problems when you enter a room.
12. If an item is knocked over or there seems to be any problem with materials or equipment in a room (noise, smell, heat, smoke, etc.) please report it to your supervisor, the COE CHO or Facility Coordinator, and/or public safety. Use an emergency phone box or 911 from an office phone as necessary.
5.6 Employee Medical Consultation, Examinations, and Surveillance
If an employee has an adverse reaction to a hazardous chemical, then the following subsections may apply.
5.6.1 Medical Attention and Followup
The COE shall provide employees who work with hazardous materials an opportunity to receive medical attention, including any follow-up examinations which the examining physician determines to be necessary, under the following circumstances:
1. Whenever an employee develops signs or symptoms associated with a hazardous chemical to which the employee may have been exposed in the laboratory, the employee shall be provided an opportunity to receive an appropriate medical examination through the University’s Worker’s Compensation program.
2. Where exposure monitoring reveals an exposure level above the action level (or in the absence of an action level, the exposure limit) for a Cal/OSHA regulated substance for which there are exposure monitoring and medical surveillance requirements, medical surveillance shall be established for the affected employee as prescribed by the particular standard.
3. Whenever an event takes place in the work area such as a spill, leak, explosion or other occurrence resulting in the likelihood of a hazardous exposure, the affected employee shall be provided an opportunity for a medical consultation. Such consultation shall be for the purpose of determining the need for a medical examination.
4. All medical examinations and consultations shall be performed by or under the direct supervision of a licensed physician and shall be provided without cost to the employee, without loss of pay and at a reasonable time and place.
5. Information provided to the physician. The employer shall provide the following information to the physician:
- The identity of the hazardous chemical(s) to which the employee may have been exposed;
- A description of the conditions under which the exposure occurred including quantitative exposure data, if available; and
- A description of the signs and symptoms of exposure that the employee is experiencing, if any.
5.6.2Physician’s Written Opinion
For a Physician’s examination or consultation of employees as required under 8 CCR 5191, the COE will obtain a written opinion from an examining physician that includes the following information:
- Any recommendation for further medical followup.
- The results of the medical examination and any associated tests, if requested by the employee
- Any medical condition which may be revealed during the examination which may place the employee at increased risk as a result of exposure to a hazardous chemical found in the workplace
- A statement that the employee has been informed by the physician of the results of the consultation or medical examination and any medical condition that may require further examination or treatment.
The written opinion cannot reveal specific findings of diagnoses unrelated to the occupational exposure.
5.6.3 Student Workers with Potential Adverse Health Effects from Hazardous Chemicals
Student laboratory workers who exhibit signs and symptoms of adverse health effects from a work-related exposure to a hazardous chemical should notify their immediate supervisor and then report to the Student Health Center or personal physician. Refer to the Injury and Illness Prevention Program (IIPP) for procedures on how to obtain medical evaluations.
5.6.4.Medical Surveillance
Medical surveillance is the process of using medical examinations, questionnaires and/or biological monitoring to determine potential changes in health as a result of exposure to a hazardous chemical or other hazards. Certain Cal/OSHA standards require clinical examination as part of medical surveillance when exposure monitoring exceeds an established Action Level or Permissible Exposure Level (LEL).
Occupational medical service providers will conduct medical surveillance services. Medical surveillance is required of employees who are routinely exposed to certain hazards as part of their job description (such as asbestos) and may be offered to other employees based upon quantifiable or measured exposure.
The following chemicals may be monitored through a medical surveillance program:
- Asbestos
- Benzene
- Formaldehyde
- Lead
- Methylene Chloride, and
- “Particularly Hazardous Substances.”
In addition, both noise (noise testing as specified in a Hearing Conservation Program) and respirator use (inhalation monitoring in Respirator Protection Program) can be monitored through a medical surveillance program when the respective programs are required.
5.7 Reproductive Health Policy
Male or female, you should never work with a chemical without knowing how it may affect the reproductive system, and the length of time the material could remain in your body if ingested, inhaled, or absorbed. The use of some agents should be stopped well in advance of conception.
Pregnant women and those who plan to become pregnant are strongly encouraged to consult their physician regarding the evaluation of workplace hazards as they relate to reproductive health and fertility. The physician should be provided with specific information regarding type of work, chemicals used, SOPs, and be provided SDS for all chemicals.
If working with other hazardous materials, you may find the following documents helpful:
- NIOSH Pocket Guide to Chemical Hazards," from the U.S. Department of Health and Human Services
- SDS online access (see COE CHO)
Please feel free to contact your supervisor, COE CHO, or EH&S with any further requests for information required by you or your physician regarding reproductive hazards in the workplace.
5.8 Fume Hood Requirements
5.8.1 Overview
Chemical fume hoods constitute an important safety resource for COE personnel. See Figure 1 for a standard fume hood diagram. Hoods are used instead of strap-on respirators to protect personnel from airborne chemical hazards. When used PROPERLY hoods provide protection from hazardous vapors, gases, fumes, mists, and dusts that may arise from the materials being handled.
General-use chemical fume hoods must be inspected/surveyed annually by the COE CHO or designee. The inspection/survey process consists of quantitative airflow measurement, qualitative inward airflow check, check of the permanent, quantitative, airflow indicator, label check, lighting check, noting special use/conditions, and certifying the inspection/survey label and data sheet. Any hood that fails the airflow tests must be immediately posted "Out of Service." The data sheets will then be reviewed by Safety personnel to generate a list for hood repairs and prioritizing the repairs with respect to employee/student safety.
Cal/OSHA mandates that the hood-inspection records (the completed data sheets generated by the process) be retained for FIVE YEARS. Original data sheets or similar documentation (computerized data) are retained in the COE Safety Office. Hoods must be re-surveyed after critical hardware has been changed or repaired (motor replacement, change in pulley size, etc.) or if inadequate performance is suspected (as evident by the airflow indicator).
5.8.2 Fume Hood Guidelines
General guidelines for the use of a chemical fume hood are listed below. All 12 considerations below MUST be understood and followed when using a hood to protect you from harmful concentrations of hazardous chemical (levels above the Cal/OSHA Threshold Limit Value).

2. A continuously operating airflow indicator must be present, operational and demonstrate proper airflow. Most COE hoods are equipped with Vane-o-meters shown below in Figure 2. Verify airflow is in excess of 100 LFM prior to each use.
3. Use the hood with the sash no higher than the mechanical stop or point indicated by the "arrow" stickers. Temporarily raising the sash above the arrow/stop position (to facilitate equipment or container movement) may not be done for more than a few minutes or when hazardous chemicals are in use. Keep the hood sash closed when not using the hood.
4. To ensure proper performance, minimize the amount of material inside the fume hood. An item as large as a basketball can cause an airflow “dead zone” preventing the hood from meeting proper airflow standards and allowing hazardous emissions out into the lab. All items in the hood should be no closer than 6 inches from the front airfoil. In addition, maintaining 1 inch of space between items and under large objects
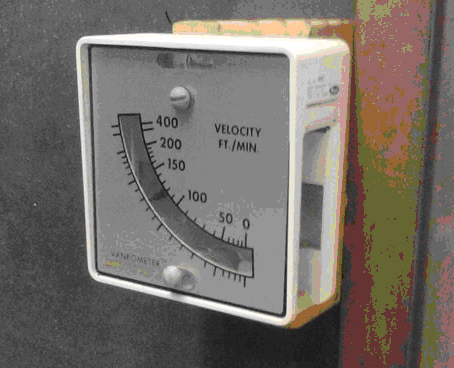
5. Do not manipulate hazardous chemicals in a malfunctioning hood as you will be exposed to the material being handled. In the event of a hood failure or ventilation malfunction, STOP WORK IMMEDIATELY, close the hood sash and inform others in the room. Report any hood problems promptly to your supervisor, COE CHO, or campus EHS.
6. In the event of fire, close the sash (if safe to do so) and exit room. Do not push the Emergency Exhaust button! Use the hallway fire alarm as appropriate.
7. Do not use the hood to intentionally dispose of (evaporate) hazardous chemicals. Containers of volatile materials in the hood must be kept closed when not in use.
8. Hood use for a Cal/OSHA-regulated carcinogen requires more stringent standards.
9. Hoods should be cleaned periodically. Annual cleaning is recommended.
10. Hazardous waste containers in hoods must be inside a secondary container tray, tub, or bucket.
11. After addition of large items, the airflow must be re-surveyed.
12. Users may NEVER put their head into the hood.
5.8.3 Fume Hood Inspection Procedure
This hood check procedure is to be performed by trained personnel wearing appropriate PPE (ex., lab coat, goggles and disposable gloves). The inspector should minimize handling items inside the fume hood. If an item in the hood obstructs airflow, the inspector is not obliged to move the offending item even if the item in question causes the hood to "fail" the airflow test.
If the hood fails due to inadequate air flow of 100 liters per minute (LPM), then the inspector should move the sash lower in an attempt to attain proper flow (no lower than the 12 inches minimum).
1. Label check:
Make sure that required Chemical Fume Hood Inspection sticker is in place. Re-label as needed. Place the new label over the old one to minimize clutter. If an exhaust fan code or use label is present, make sure it is legible.
2. Airflow measurement:
a) Move sash to the "arrow" sash-height indicators if present or to the "hood stop" at the top. Take readings at nine sample points (at least 1 inch from the opening perimeter) to determine if airflow is over 100 LPM. Rotate the measuring device (velometer, Vane-O-Meter, etc.) as needed to obtain the highest flow value. Do not block airflow with your body. Recall that items in the hood can create airflow zones of less than 70 LFM. If the averaged airflow is less than 100 LPM, the sash may be lowered until the average LFM meets the required threshold (note: 12-inch minimum opening). If the sash opening has been changed, the arrow indicators must also be changed at this time.
b) To perform a qualitative airflow measurement using chemical smoke, slowly puff smoke across the face of the hood. The smoke must be pulled into the hood with any blowback of smoke being grounds for failure.
3. Airflow Indicator check using a Vane-o-meter:
a) This indicator must remain firmly attached, level and read accurately. Use a brush to clear dust from the device being careful not to disturb the fragile vane. If it is damaged, the vane must be replaced.
4. Hood lighting check:
a) Ensure that the fluorescent lights are functioning and record the results. Replace as needed.
Immediate response is required if the following events occur with a fume hood:
a) If airflow is less than an averaged 100 LFM upon testing or if motor issues occur, post the hood with a "DO NOT USE; Inadequate Airflow" warning sign. Contact the COE CHO or Facilities to coordinate service for a hood.
b) If unsafe practices are encountered (unlabeled hazmat, incompatible chemicals, open containers, waste problems etc.) when attempting to test, contact the COE CHO who will coordinate with the responsible party, and the department chair to correct the issue.
5. Documentation/Recordkeeping:
a) If the unit passes, initial and date the hood inspection tag. If it fails, mark "FAILED" and the test date.
b) Complete the Hood Inspection Data Form and note any special problems in the "comments" section.
c) The COE CHO will prioritize the findings and coordinate repairs for problems as appropriate. The COE CHO will file the survey data sheets per the Cal/OSHA five-year record retention mandate.
5.9 Use of Risk and Safety Solutions (RSS) Software
COE CHO is coordinating the implementation of a chemical software system at COE which is designed to improve safety and facilitate regulatory compliance in campus laboratories where hazardous chemicals are used. The software was developed by the University of California Systems in order to implement risk management and safety tools. The software has been used extensively throughout UC campuses and medical centers and has been adopted by the California State University System for implementation. The software system is organized into the following three integrated modules.
5.9.1 Risk Assessment Module
This tool allows principal investigators to identify hazards related to their research and share this and other critical safety information about these hazards with the members of their lab. You can start your assessment today by signing into https://csu.risksafety.solutions/signin using your campus email and then entering your single sign-on information. A window will come up with the icons shown below and then click “Assessment”
5.9.2 Chemicals Management Module
A chemical inventory management tool will use a barcoding system to quickly add chemicals to an inventory. It includes a library of chemicals that are referenced to populate chemical details, like hazards and first aid information. The module is available in a phone app as well as for tablet or desktop.
5.9.3 Inspections Module
A flexible, customized tool that manages the scheduling, completion and long-term tracking of safety inspections, it is available for phones, tablets, and desktops.
Implementation of this system at COE is required for all labs utilizing chemicals. For non-lab areas using chemicals such as a machine shop, the chemical inventory can be kept using MSDSonline. The COE CHO will assist with training and support during implementation of RSS.
Safety information is conveyed with the CSULB website, targeted emails, and through verbal communications and trainings. The following websites can be used to obtain safety information pertaining to COE and CSULB campus:
COE and CAL/OSHA require the development and use of Standard Operating Procedures (SOP) when dealing with hazardous materials and hazardous operations. An SOP is a written set of instructions that document how to safely perform hazardous work or processes to ensure that projects are conducted in a safe and consistent manner.
SOPs may focus on any of the following: Processes (e.g., novel nanomaterial synthesis, distillation, laser sintering) Hazardous chemicals (e.g., carbon monoxide, hydrofluoric acid) Class of hazardous chemicals (e.g., organic solvents, pyrophoric material, heavy metals)
An example SOP for concentrated mineral acids can be found in Appendix D. Sample chemical SOPs created by other educational institutions can be found here: https://www.ehs.ucla.edu/documents/Laboratory
Alternative SOP formats are acceptable for lasers and other equipment or processes. The only requirement is that the SOP ensure a safe, predictable outcome when students, faculty, and staff are working with hazardous chemicals or conducting hazardous operations. SOPs shall be reviewed and approved by the COE CHO and/or EH&S.
Safe handling, use, and disposal of hazardous materials prevents injuries and incidents. Tracking of chemicals on campus will be performed through the RSS system for laboratories and the MSDSOonline system for non-lab spaces. Faculty are responsible for the inventory, storage, use, and disposal of any hazardous chemicals acquired by the personnel they supervise.
The following materials are currently restricted on campus: Cal/OSHA regulated carcinogens, Risk Group Level 3 or 4 biohazardous materials, explosives, DEA-regulated chemicals, human blood and blood products, and highly unstable/water reactive materials. Contact COE CHO for details. Personal transport of hazardous materials to CSULB or from CSULB to an offsite location must have approval from both the COE CHO and the EH&S Director.
8.1 Particularly Hazardous Substances (PHS)
Substances that pose significant threats to human health are classified as "particularly hazardous substances" (PHS). The OSHA Laboratory Standard and Cal/OSHA regulations require that special provisions be established to prevent the harmful exposure of researchers to PHS, including the establishment of designated areas for their use.
Particularly hazardous substances are divided into three primary types:
- Acute Toxins
- Reproductive Toxins
- Carcinogens
8.1.1 Acute Toxins
Substances that have a high degree of acute toxicity are interpreted by Cal/OSHA as being substances that "may be fatal or cause damage to target organs as the result of a single exposure or exposures of short duration.” These types of chemicals, associated waste, and storage containers must be handled with care to prevent cross contamination of work areas and accidental contact. These chemicals must be appropriately labeled, and any empty containers must be triple-rinsed, with the rinsate discarded as hazardous waste. Waste rinsate shall not be disposed of into the sanitary sewer system.
8.1.2 Reproductive Toxins
Reproductive toxins include any chemical that may affect the reproductive capabilities, including chromosomal damage (mutations) and effects on fetuses (teratogenesis). Reproductive toxins can affect the reproductive health of both men and women if proper procedures and controls are not used. For women, exposure to reproductive toxins during pregnancy can cause adverse effects on the fetus; these effects include embryolethality (death of the fertilized egg, embryo or fetus), malformations (teratogenic effects), and postnatal functional defects. For men, exposure can lead to sterility.
Examples of embryotoxins include thalidomide and certain antibiotics such as tetracycline. Women of childbearing potential should note that embryo toxins have the greatest impact during the first trimester of pregnancy.
Because a woman often does not know that she is pregnant during this period of high susceptibility, special caution is advised when working with all chemicals, especially those rapidly absorbed through the skin (e.g., formamide).
Pregnant women and women intending to become pregnant should consult with their laboratory supervisor and their physician before working with substances that are suspected to be reproductive toxins.
8.1.3 Carcinogens
Carcinogens are chemical or physical agents that cause cancer. Generally, they are chronically toxic substances; that is, they cause damage after repeated or long-duration exposure, and their effects may only become evident after a long latency period. Chronic toxins are particularly insidious because they may have no immediately apparent harmful effects.
- Select Carcinogens as defined in CCR Title 8 § 5191 include any substance regulated by Cal/OSHA as a carcinogen, any substance listed under the category “known to be carcinogens” in the Annual Report on Carcinogens published by the National Toxicology Program (NTP), any substance listed under Group 1 (“carcinogenic to humans”) by the International Agency for Research on Cancer Monographs (IARC) (Volumes 1-48 and Supplements 1-8); or any substance listed in either Group 2A or 2B by IARC or under the category, “reasonably anticipated to be carcinogens” by NTP.
- Regulated Carcinogens are those select carcinogens regulated by Cal/OSHA as carcinogens and fall into a higher hazard class and have extensive additional requirements associated with them. The use of these agents may require personal exposure sampling based on usage. When working with Regulated Carcinogens, it is particularly important to review and effectively apply engineering and administrative safety controls as the regulatory requirements for laboratories that may exceed long term (8 hour) or short term (15 minutes) threshold values for these chemicals are very extensive. Approval must be granted by COE CHO prior to commencing work with this class of chemicals.
- Listed Carcinogens are a special subset of Regulated Carcinogens and are listed in CCR Title 8 § 5209. The use of these materials is strictly regulated and must be registered with COE CHO and Campus EH&S.
8.2 Designated Areas for PHS
Designated area(s) for use of particularly hazardous substances must be formally established by developing SOPs and posting appropriate signage. This designated area(s) may be an entire laboratory, a specific work bench, or a chemical fume hood. When particularly hazardous substances are in use, access to the designated area shall be limited to personnel following appropriate procedures and who are trained in working with these chemicals.
Access to areas where particularly hazardous substances are used or stored must be controlled by trained employees. Working quantities of particularly hazardous substances should be kept as small as practical and their use should be physically contained as much as possible, usually within a laboratory fume hood or glove box. It is the responsibility of each Principal Investigator, or their designee, to train and authorize their staff for these operations and to maintain documentation of this training and authorization.
Signage is required for all containers, designated work areas and storage locations. The signage must state the following as appropriate for the specific chemical hazard: “DANGER – (CHEMICAL IDENTIFICATION) – MAY CAUSE CANCER”
Entrances to designated work areas and storage locations of Listed Carcinogens must also include signage stating “AUTHORIZED PERSONNEL ONLY.” Work surfaces should be stainless steel, plastic trays, dry absorbent plastic-backed paper, chemically- resistant epoxy surfaces, or other chemically impervious material.
Protocols, procedures, and experiments must be designed and performed in a manner to safely maintain control of the particularly hazardous substances. Laboratory personnel must specifically consult with their PIs if a special hazard is involved (e.g., material under pressure) or if they are uncertain of the potential hazards.
8.3 Personal Protective Equipment(PPE)
PPE must be sufficient to protect eyes and skin from contact with the hazardous agents. Chemical splash goggles, lab coat, long pants, closed toe shoes, and gloves are required when working with PHSs. Flame-resistant lab coats may be required if the chemicals being used are flammable or when handling pyrophoric chemicals outside of a glove box.
Refer to the specific chemical’s SDS and SOP for specific information on additional PPE and glove selection. Contaminated PPE and clothing must be disposed of as hazardous waste.
8.4 Engineering Controls for PHS
Benchtop work with PHS is prohibited. Containment systems (such as fume hoods or glove boxes) must be used. Laboratories and rooms where PHS are used must have local exhaust ventilation such as chemical fume hoods or be used/stored in glove boxes for containment purposes. Air from these ventilation systems must be vented externally; recirculation is not permitted. Doors providing access from public areas must be kept closed.
8.5 Special Handling and Storage Requirements
Particularly hazardous substances must be stored in a designated area and used in a manner that will minimize the risk of accidental release (e.g., capped tightly, use of chemical resistant secondary containment, whenever possible). Laboratory personnel should remove chemicals from storage only as needed and return them to storage as soon as practical.
Chemicals should be segregated from incompatible materials, as described in the COE General Safety Awareness Training Presentation. The use of PHS must be confined to an established designated area.
Additional requirements for the safe storage of a specific chemical may be found in the manufacturer’s instructions or in the SDS. When transporting chemicals beyond the immediate laboratory environment, containers should be protected from breakage by using a bottle carrier or other effective containment.
Contact COE CHO for guidance on the planned use of chemicals that may require further controls.
8.6 General Chemical Spill
In the event of a hazardous materials spill, the following procedures should be conducted. If it is an inhalation hazard, extremely hazardous, or you don’t know what it is, warn people and vacate the premises. Inform everyone who may be in danger that there is a spill, and to leave the danger zone immediately. Close the area doors and contact University Police via callbox/911 or pull the building fire alarm if area evacuation is necessary.
Call COE CHO or EH&S to report the spill. Section 1.1 for contact information. Request assistance as needed.
Identify the spilled chemical if safe to do so. If you do not know its hazards (flammable, corrosive, poison etc.), FIND OUT NOW. Ask someone who works with the chemical or Issue Room/Safety people and/or read the SDS BEFORE proceeding. Even a few grams or milliliters of some materials pose an inhalation hazard and must only be cleaned up by professionals wearing self-contained breathing gear and HAZMAT suits.
Spill cleanup: If it is safe to remain in the room, you know an overexposure is not possible, the spill is smaller than 1 liter/500gm, and you are capable of safely cleaning it up yourself, proceed as follows (stop if you feel affected by exposure):
1) If spilled material is flammable, extinguish all sources of heat and keep sparks away.
2) Keep people away from the spill.
3) Put on fully enclosed chemical splash goggles.
4) Put on two pair of gloves; check glove chart to be sure of protection from the chemical.
5) Stop the flow of the spill and utilize absorbent materials, pads, or pillows. Do not use paper towels unless the spill is very small and not an oxidizer.
6) Carefully place soaked materials into a compatible bag/container that can be sealed.
7) Put the closed container in a hood. Label it with a yellow “Hazardous Waste Label.”
8) Decontaminate surfaces/tools promptly. Use an appropriate cleaning agent. Contaminated cleanup materials go in the waste container too. If in doubt, contact EH&S, who will perform the clean-up.
In the event of direct skin contact with a particularly hazardous substance, the affected person must shower or flush the affected areas for a minimum of 15 minutes. Emergency eyewash stations should be used to more effectively flush eyes or other mucous membranes when involved.
Complete an INCIDENT REPORT form (attained by the COE CHO). Alternately call/visit COE CHO and relay what happened.
8.6.1 Acid Spills
For acid spills, call COE CHO for an acid spill kit if not readily available at your location. The following are instructions for a spill cleanup of a small (< 50 ml) release in a chemical fume hood:
Warn others and isolate the spill by closing the hood sash. Make sure you are wearing acid-resistant gloves, chemical splash goggles lab coat, Tyvek suit/sleeves or other appropriate protective clothing. Proceed with cleanup by placing an absorbent pad on the spill to contain the liquid. Remove acid pad and place into plastic zip-lock bag. Sprinkle acid neutralizer around perimeter of spill, then cover spill completely with neutralizer. Heat will be generated as neutralization occurs. The absorbent pad should have soaked up much of the liquid, so you are neutralizing the residue such that the hood may be safely used again. Stir with plastic scraper to increase neutralization effect. Wait at least 20 minutes for mixture to cool.
After 20 minutes, scoop up neutralizer/acid mix and place in plastic Ziplock bag for disposal. Use acid pads for further cleaning as necessary. Fill out yellow waste label and place on plastic bag. Call COE CHO for waste pickup. Confirm surface pH is neutral using test strip and small amount of water. Contact COE CHO or campus EH&S to report larger spills, spills outside the chemical fume hood or if you are incapable of performing or have not received training in this procedure.
8.7 Routine Decontamination Procedures
To limit the spread of contamination, laboratory work surfaces should be decontaminated at the conclusion of each procedure and at the end of each day on which PHS are used.
All equipment should be decontaminated before removing it from the designated area; this decontamination should be carried out in a glove box or fume hood where practical.
Contaminated PPE must not be removed from the designated area until properly decontaminated; after working with these chemicals, gloves must immediately be removed and disposed of as hazardous waste and hands and arms washed with soap and water. Contaminated PPE shall be bagged and sealed in polypropylene or other impermeable container and labeled.
8.8 Regulated Carcinogens and Report of Use Requirements
Regulated Carcinogens are a specific subset of select carcinogens which have special additional requirements associated with their use under certain circumstances. Every effort should be made to keep exposure levels below regulatory threshold limits by using engineering and administrative controls, appropriate PPE and following customized SOPs designed to reduce exposure. If exposures cannot be kept below regulatory thresholds, work shall cease until measures can be put in place to reduce exposure to acceptable levels. Before work may resume, additional requirements may include:
- Required medical evaluations.
- Additional documented training.
- Use of respirators with required initial and ongoing training, medical evaluations, and maintenance documentation.
- Additional documented hazard evaluations.
Listed Carcinogens are a further subset of regulated carcinogens. A list of these compounds can be found in CCR title 8 section 5209 (e) (1) (D). An evaluation will be completed to assess safety requirements for groups that use these materials.
Report of Use Requirements must be met for each group when they:
- Begin the use of, or make significant changes to, existing use of any Listed Carcinogen.
- Use Regulated Carcinogens such that there is a reasonable expectation that exposure limits may be exceeded.
- Occur during an emergency in which employees have been exposed to any Regulated Carcinogen.
Whenever a chemical is taken from its original container, a secondary label is affixed to the new container to identify contents and any relevant hazards. The standard COE label is shown below and uses a DOT (Department of Transportation) based container labeling scheme with the addition of GHS pictograms.

- Product ID: Use the full name. Do NOT use abbreviations such as ETOH. Instead write the full name Ethanol. Hazard Statement: Write the hazard word shown below that was on the original container. Place a check mark on the appropriate symbol.
- Make sure any old, inappropriate labels are completely unreadable (you may erase, deface, or remove labels).
- Permanently labeled bottles may not be used for a different material (your label may fall off or your ink may wash off to show the old wrong label).
9.1 Container Labeling Addendum

Material Labeling Program Supplementary Information
1. Treat materials that bear any hazard warning as toxic.
Avoid inhalation, skin contact, and contamination of surfaces. Do not mix or store them with other materials unless you know the reactive properties.
Employees and students are required to know the hazardous properties of each material they handle.
2. Any properly labeled material may have additional hazardous properties.
The safety-trained faculty or staff person in charge of your workplace will be able to provide more specific chemical safety information (as is contained in Safety Data Sheets (SDSs) and other sources).
- Toxic effects of chemicals are varied. Materials marked “POISON,” for example, may be toxic through very different mechanisms. Route of entry, exposure time, temperature, your physical condition, etc. all influence toxic effects.
- Target organ. Many toxic agents focus on specific tissue, organs, or organ systems. The affected organ can be remote from the point of exposure. The eye, for example, can be affected from skin exposure to methanol.
3. Compatibility cannot always be determined by the hazard label.
While hazard labels indicate the gross hazard class, do not assume that all materials of the same hazard class are compatible (e.g. acids and bases are both labeled as corrosive). Refer directly to SDS-type information or to the College employee in charge of the area.
4. Spills of hazardous chemicals must be handled by qualified persons.
Contact COE CHO or call Campus EHS if you have ANY DOUBT about the severity of a chemical spill. Even a few milliliters or milligrams of some materials require trained persons using self-contained breathing equipment to avoid overexposure.
5. The college labeling procedure is written and is on the COE Safety website.
College employees and many laboratory students have been instructed in proper labeling as part of their introductory safety training. The details for the label system are among the official “Right-to- Know”/“Hazard Communication procedures” adopted by the College and/or University.
Hazardous wastes generated in the laboratories must be handled, labeled, and properly stored according to California regulations (22 CCR 66262) prior to removal by Campus EH&S.
10.1 Control of Waste-Producing Operations
Faculty (course coordinators, thesis advisors, principal investigators, etc.), staff (technicians, trades persons, supervisors, researchers, etc.) and administrators (program directors, deans, chairs) must anticipate and prepare for the responsible management of any hazardous waste generated from the campus activities they perform and/or oversee. Cal/OSHA has strict requirements regarding who may handle hazardous waste; you and your personnel may handle ONLY the waste generated by yourselves at your own worksite (usually a lab).
This written procedure is designed to help campus personnel fulfill this obligation. Nearly any use of a hazardous chemical can generate hazardous waste. Regulated hazardous waste can be created from “non-hazardous” materials. When hazardous waste must be produced, COE CHO will assist in the development of a process-specific plan to ensure safety and regulatory compliance. If possible, a non-hazardous or less-hazardous option will be proposed.
10.1.1 Generation Point Hazardous Waste Containers
Selection of an appropriate container or containers to hold the waste routinely generated by workplace operations is a critical step. If in doubt, contact COE CHO/Facilities at 5-8746 or EH&S at 5-2283 for details.
Sound, intact containers, appropriate for the waste, may be used over and over again for the same waste stream (emptied by specifically trained personnel into larger waste containers and then returned to the generation site) or they may be one-use containers (the disposition of unwanted emptied waste containers is the responsibility of the hazardous waste contractor). The following container selection/use guidelines must be observed at all times:
a. Container material: The container must be compatible with the waste, i.e. No acids in steel containers, no gasoline in Styrofoam, no picric acid or perchloric acid solutions in lead soldered or zinc-coated containers. No food or drink containers may be used.
b. Container condition: The container must be in sound condition including the closure(s) and gasket(s) as appropriate. No brittle, degraded plastics, structurally corroded metal, etc.
c. Container closure: The container must be equipped with a leak proof mechanical closure such as a threaded cap. The cap must be equipped with a gasket that contains the material when being carried or if it is tipped over. Cap threads must match the container. Friction fit stoppers or film seals are unacceptable.
d. Container size: Whenever possible, the container size should be matched to the volume of waste generated within 6 months. 100 ml of waste liquid in a 5-liter bottle can be a very wasteful situation as some waste contractors simply place the bottle in a drum rather than transfer/consolidate the material. Always leave room in the full container to allow for expansion. In the case of extremely hazardous chemicals; however, a small volume, including an un-rinsed "empty" container, can be an acceptable waste item.
e. Container spill control: Hazardous waste containers shall be stored in secondary containment. Fume hoods themselves do not function as secondary containment units. Secondary containment units are often available at no cost through the COE CHO.
10.1.2 Required Labeling for Hazardous Waste Containers
State and federal EPA regulations are very strict as to the labeling of hazardous waste. Never write the word “WASTE” on any container. For this reason, self-adhesive EPA-compliant Hazardous Waste Labels, shown below, are distributed by the CHO to COE faculty and staff.

The person who sets up the waste collection container must write in information by hand, check boxes and circle categories to complete the label. Completely spell out waste components, do not use abbreviations. Waste identification must be understood by non-science personnel, including custodians and trades.
When waste containers are too small for the COE Hazardous Waste label, put the completed label on a 4 mil reclosable bag, add containers to bag, and zip closed. Bags are available from COE CHO. Contact the department issue room or the COE CHO for more information regarding the data required on the label or any other waste related question.
Instructions for Completing the Hazardous Waste Label: Please have a label in your hand as your read this information.
1. Start date: The date waste was first placed in the container or date the material was designated as waste must be indicated. Mark the date directly on the label. IN NO CASE MAY GENERATION POINT WASTE BE ACCUMULATED FOR MORE THAN NINE MONTHS -- EVEN IF THE CONTAINER IS NOT YET FULL. Request a pickup by notifying the COE CHO when the waste is six months old. This will prevent the risk of costly fines by regulatory agencies.
2. Name/identity of the waste material: The box marked “This container is to be used for the collection of:” requires a general name for the waste. This name must, where possible, be a recognized chemical or product name (such as "toluene" or "pump oil"). When the waste consists of a mixture of materials (such as "halogenated solvents", "animal preservative", or "HPLC waste") each component of the mix must be listed, and the approximate percent of the total mixture volume indicated. If the mixture contains more than 10 components, write the other components on an attached sheet. For example:
This container is to be used for the collection of: “Mixed solvents"
Components: "acetone 60%”, “isopropanol 5%”, “chloroform 5%”, “water 30%"
Below the “This container” box, circle the properties that apply to the waste. In the case of this example, circle “Solvents (non-halogenated)” and “Solvents (Halogenated).”
3. Physical state: Check the box to indicate Solid, Liquid or Gas. This MUST be done -- even if the waste is in a clear bottle and the physical state is obvious.
4. Hazard(s): Check appropriate box to indicate if Flammable, Oxidizer, Corrosive, Poison, etc., as appropriate. Hazard information may be taken from the original product label, ask the CHO (hazards assigned per DOT: 49CFR Sect. 172.101). For Flammable, Poison and perhaps Carcinogen would be appropriate. 5. Contents: As discussed in Item 2 above, use these 10 spaces to list the Components and Amount in % of the waste.
6. Faculty or staff name: The name of the faculty, staff or administrator responsible for the contents and oversight of the waste container must be indicated on the label. Please note that official responsibility for effective, ongoing oversight of a waste generating operation cannot be delegated to a student. The person listed is responsible for ensuring compliance and conveying these hazardous waste guidelines to everyone who generates waste. Having a person’s name on the label also facilitates timely return of re-usable waste containers.
7. DEPT (Department): Write in the department responsible. It may be an academic department, College, trades group (ex., Paint Shop, Auto Shop, Grounds, etc.), Animal Facility, etc. The department that acquired the original material is typically the group responsible for the waste created by its use. 8. Room #: List the room/location where the waste was created. Only waste generated on the CSULB campus may be managed by the CSULB program. Transport of waste to the campus from elsewhere is prohibited.
9. Acc. Fac. S.D.: Generators do not use this box. Campus Safety personnel indicate here when a full container has been moved to an approved on-campus storage area.
10.1.3 Generation Site Waste Management Practices
The faculty and/or staff considered responsible for a given waste-generating process should regularly examine the container(s) and monitor compliance. The responsible person must ensure that:
- All persons adding waste are trained in waste compatibility and policies
- All material added to the container is chemically compatible
- Hazardous waste is collected -- not dumped in a sink or trash can
- The container is sound and compatible with the waste
- The container is kept closed at all times, except when adding waste
- The container is kept in a containment tub, tray or other type of secondary containment
- The container, label and any log sheet list contents and amount.
- Any spills are dealt with promptly.
- The COE CHO is notified when (1) The container is full, or (2) The six-month anniversary date (from first use) is approached, whichever comes first.
All laboratory personnel who work with or may be exposed to particularly hazardous substances (PHS) must be provided laboratory-specific training and information by the PI or their designee prior to beginning their initial assignment. Laboratory-specific training should cover specific policies and procedures, SOPs, etc. and is in addition to the basics covered in the General Safety Awareness Training presentation. Records of laboratory-specific training must be maintained in the laboratory and should include an outline of the topics covered. It is recommended that training documentation be maintained in Laboratory Safety Notebook.
Training shall include:
- The hazards/toxicological effects associated with the chemicals being used.
- Routine procedures and decontamination methods.
- Emergency response practices and procedures.
- Methods and observations for detecting the presence or release of hazardous chemicals.
- Available protection measures, including engineering controls, appropriate work practices and (PPE).
- A review of written SOPs, SDSs and the CHP.
- A review of applicable policies.
Annual refresher training is required for particularly hazardous substances. Also, whenever there is a change in process, procedure or equipment training is required to update affected lab personnel. Written records must be maintained for each training session and stored in the EHS-managed Share Drive.
Labs shall be locked outside of normal work hours (7 a.m. to 5 p.m. Monday through Friday) and when unoccupied. Laboratory supervisors will determine the policy of locking doors during normal working hours.
Entry to all research (non-teaching) labs in the COE is restricted to trained, authorized key holders and other individuals authorized by the faculty in charge. Escorted guests with appropriate training or advisement may be allowed into a lab by the laboratory supervisor, appropriate administrator, or staff member in charge.
Supervising faculty/staff shall create a list of authorized individuals (see Appendix A). This list is to be posted on the interior of the laboratory entry door(s) and shall be updated as safety-trained personnel join or leave the lab.
After-hours work (i.e., Saturday/Sunday 8 a.m.-10 p.m. and Monday through Friday 5-10 p.m.) requires permission from the laboratory supervisor. Hazardous work, as determined by the laboratory supervisor and COE CHO, requires approval by the appropriate COE Chair (See Table 1.1).
Students (graduate and undergraduate) may never work alone in the laboratory outside of normal work hours. COE requires a minimum of two people in a lab when working after hours to ensure help can be called if one person has a medical emergency.
Key holders are responsible for the security of their keys. Keys shall remain on their person or otherwise secure when working in lab. Keys are not to be left on tables, desks, benches, or other areas in plain sight. Loaning of state keys is strictly regulated by California Penal Code 469. Keys to common-use areas shall be stored out of sight in secure locations within labs.
If an unauthorized individual gains access to your lab, inform them of the security policy and politely ask them to leave the lab. If needed, call Campus Police 911. Do not place yourself in danger by aggressively confronting unauthorized people. Let the police handle it.
This plan is to be reviewed annually and the following change log details updates that occur to the plan. Reviews will be coordinated by the COE CHO and incorporate input from COE Dean, Associate Deans, Faculty Safety Committee, and COE Facilities Coordinator.
Date | Reviewer | Changes |
---|---|---|
April 21, 2020 | Glen Seymour and John McCabe | Initial CHP Release |