Mechanical Engineering Teams Show Off Senior Design Projects
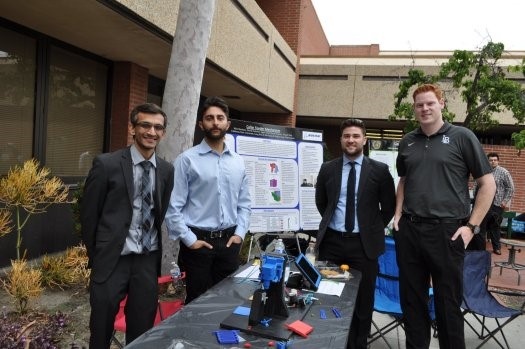
The two-semester capstone courses, taught by Assistant Professor Surajit Roy and Professor Chris Beyer, emphasize theory and practice of modern design and manufacturing. During the first semester, students focus on the concept and embodiment design, and during the second semester, concentrate on project implementation.
Eight industry and alumni judges ranked the projects and issued Most Innovative Design Awards to two teams, one that designed an automatic Collar Feeder Mechanism and another that designed an Auto Calibration Drop Tester. Both projects were supported by Boeing and represented potential solutions to real-world industry problems.
The Collar Feed Mechanism team presented a design that would allow the Collar Feed System to fit within a robot when in the collapsed, telescoping, and extended positions. The project has the potential to revolutionize aircraft wing assembly, creating efficiency and reducing the foreign object debris (FOD) inside the aircraft wing, where fuel is stored. Members of the team are Yousef Aziz, Matt Barnhart, David Lepore, Jigar Patel, and David Pedersen.
The Auto Calibration Drop Tester team was tasked by Boeing to automate the sealant calibration process. Currently, sealant is dispensed onto a scale and the mass extruded compared in a set time-period with the desired mass. Parameters such as pressure are changed manually to have the desired mass/flow rate. The team members are Maximilian Chiecuhin, Andrew Fiallo, Ryan Touch, Benedict Ward, and Faith Yu.
The Most Popular Design Award went to Matthew D. Donoghue, Jenna N. Hagen, and Mathew M. Major, who took on the challenge to develop an anti-loop technology to complement contemporary turntables. The device works passively and continuously to identify the occurrence of looping. Upon identification, this device will safely advance the stylus’ position two to five grooves as to move ongoing play beyond the record’s defect and end the looping condition. As the system looks for looping it will repeat this correction process as necessary to advance beyond the defective zone of the record.
The 24 other teams are:
Roll On Unit : The team was tasked by Boeing to propose a modernized method to bond satellites to bases with a thermal insulation compound while also minimizing the presence of air bubbles. This effort defined the process to “roll on” different shapes to the bus without air entrapment. After establishing the procedure, the project has been replicated using a robotic system and defines a consistent, void-free process.
Team Members: Logan Furlong, Daniel Mittelstein, Jordan Jubile, Jennifer Neithardt, and Emily Sanders
Industry supporter: Boeing
Surface Cleaning Device: Surface cleaning is performed at Boeing to precise specifications using flammable solvents. The team was challenged to investigate how many wipes are needed to achieve the required cleaning level, the amount of solvent used, and the LEL (Lower Explosion Limit) is achieved. The goal was to develop a procedure to reduce the amount of flammable vapors in the confined space by minimizing the amount of solvent used.
Team Members: Aaron Gutierrez, Noah La Barba, Joseph Mirabal, Reyna Sandoval
Industry supporter: Boeing
Plastic Filament Extruder: The team’s task was to develop a filament extruder and spooler unit for 3D printers. The goal is to reuse 3D printing waste material by grinding it, mixing it with a certain percentage of new material pallets and extrude it with various parameters such as material diameter and spool sizes. The unit allows mixing and extruding new material combinations.
Team Members: Brian Bui, Alex Chan, Alejandro Cuevas, Ricardo Lopez, Krista Luciani, and William Luna.
Screwdriver End Effector: Boeing challenged the team to design and build a screwdriver end effector that can fasten units to a satellite structure. The end effector must weigh less than 10 pounds, have a screw feed system, and reach limited-access areas. A proper torque control should ensure precise distribution of sealant between parts.
Team Members: Chris Ponsdomenech, Aaron Raschel, Drew Schooler, Drew Yasko, and Alistair Young
Industry supporter: Boeing
Human Detection System: As humans and machines operate within the same work environment, people must be correctly identified when present so that automated systems can complete their tasks without harming people. The goal of this project was to develop a system that identifies people in a particular space and specifies their position and velocity in the collaborative workspace.
Team Members: Luis Estrada, Yasmine Garcia, Ricardo Guzman, and Toan Nguyen
Industry supporter: Boeing
Hybrid Manufacturing Head: The team was tasked to develop a wire-arc tool head for hybrid manufacturing. Hybrid manufacturing combines additive and subtractive manufacturing and is used for rapid part fabrication, prototyping, and part repair. The design requirements were given by the HAAS Mini Mill machine and the wire feeding system. The team was requested to implement a manual rotation option into the head.
Team Members: Eric Perez and Steve A. Sandoval
Industry supporter: 3D Hybrid Solutions
3D Printer For Bone Composite Material: Reconstruction of skeletal defects using custom substitutes is a solution for replacing damaged or lost anatomical bone structures to renew original functionality and restore aesthetic aspects. The currently used metal implants can lead to metal ion toxicity. 3D printing allows for rapid prototyping of complex three-dimensional models for biocompatible bone graft substitutes.
Team Members: Denzel Philip Belleza, Uzair Sumra, and Shao Ling Tan
Pipe Cleaning And Coating Device: SoCal Gas Co. asked for development of a prototype tool for both surface preparing and coating of the inside of an existing buried steel natural gas pipeline. A successful process of pipe coating will allow for repurposing pipelines to accommodate hydrogen gas usage. The team was challenged to build a scaled model for test purposes.
Team Members: Heather Leach, Jeffrey Lenz, Griffin Miller, Zeke Seraphin, Robert Zeilinger
Sponsored by: Southern California Gas Co.
Camera Sled Stabilizer: Dynamic shots are used in filming sports events where teams are constantly moving from one side to the other, but can also be used for certain movie scenes. Current technology lets the camera be mounted on a sled frame with a motor, which are then attached to a series of wires, for support and torque, allowing the camera to move along the lines made by the wires. The team had to develop a system that addresses the issue of sled stabilization (swinging) in a practical and cost-effective manner.
Team Members: Chris Miller, Nathan Nguyen, Brian Perez, Jonathan Phu, and Jayson Salvador
Automatic Planter: Gardening and agriculture still depend on manual labor. To improve efficiency and reduce labor costs of large-scale gardening and transplant procedures, a robotic system is needed that requires minimal intervention. The objective was to make a robotic planter that digs holes and transfers small plants and saplings.
Team Members: Ashton Hyman, Justin Jimenez, Walter Lezameta, Osamah Madie, Madasen Pramprasert
Hydrogen Fuel Nozzle Design Changes: Hydrogen nozzles adhere to the vehicle receptacles when used during consecutive fuel filling. The team was tasked by Toyota to determine locations where water accumulates and adheres the nozzle to the receptacle. Furthermore, the team was asked to develop design suggestions to either prevent or break the ice buildup in the nozzle.
Team Members: Laura Avellanado, Lyka Gutierrez, Patricia Herrera, Sergio Lopez, Leonardo Sanchez
Sponsored by: Toyota Motor North America
Remote Controlled Structure for Cinderella Ballet: Long Beach Ballet needed a remote-controlled undercarriage structure to move a large prop piece on stage automatically. A comparable concept exists from an earlier project; however, the dimensions needed to be converted and new adjustments were made.
Team Members: Ceejai R. Scott (Research students: Alexandra Jackson, Monica Robles and April Walsh)
Industry supporter: Long Beach Ballet
ALPHA Autonomous Pet Assistant System: Separation anxiety is common among dogs. They need interaction and simulation but are usually left alone for hours. They express their anxiety by chewing household items or barking in distress. ALPHA is an autonomous pet assistant system that interacts with the dog using a timed food dispenser holding 6 servings and a launching mechanism.
Team Members: Julian Abella, Rosie Alvarado, Josiah Barajas, Justin Heng, and Christian Garcia
Solar Sun Shade: The objective was to create a device to help start a car with a discharged battery. The group repurposed the space used by a windshield shade for a solar array to capture and store solar energy. Solar energy is stored in a micro jump starter, which can also be used to charge USB devices such as a smartphone. The jump starter will always be ready, since the sunshade is exposed to constant sunlight when in use. This device is also great for charging any USB device independently from the vehicles electronics.
Team Members: Issac Berlinski, Zach Caldero, Aileen Tran
Composite Three-Piece Helmet: The purpose of the composite three-piece helmet is to reduce the volume while optimizing the safety by satisfying DOT requirements. To achieve this goal, the helmet was made from layering carbon fiber and glass fiber fabric. The key feature of the prototype is its detachable pieces that are fastened by quarter-turn fasteners for easy assembly. The design for a detachable helmet will help future modifications of motorcycle helmets.
Team members: Phillip Au, Jose Moran, Tony Bui, Katie Diaz, Richa Tank
CO2 Reducer Using Solar Energy: Carbon dioxide is one of the primary greenhouse gases that are causing global warming. Our device uses existing carbon dioxide and reduces it into carbon monoxide while using a solar panel as its source of renewable energy. This brings forth the ability to create a carbon neutral system. The device uses two copper electrodes electroplated with cadmium which works as a catalyst to increase the production of carbon monoxide. The carbon monoxide is stored in a storage container to be used in a later process to convert it into useful products.
Team Members: Chico Baber, Jasminne Bustamante, Miguel Lopez, Jose Pimentel
Sponsored by: Southern California Gas Co.
SAE Baja Car Rear Suspension & Test Fixture: The goal of this project was to provide the CSULB Society of Automotive Engineers (SAE) Baja race team with a rear suspension that meets regulations, is easily manufactured, integrates seamlessly into their overall car design, and improves on all measurable specifications when compared to the previous design. Our design was tested through FEA analysis then validated using a testing jig. The loads applied for testing exceed anything that would be seen in any race.
Team Members: Jorge Higuera, George Bazan, George Zamora, and Pablo Gonzalez
Trash Compactor: Our team has created a trash compactor to compress the trash inside bins, reducing the potential of trashing overflowing into the streets. Our product is user friendly, portable, ergonomic, and most importantly will produce great impact on the Earth.
Team Members: Andy Duong, Nicholas Savio, Ken Le, Ryan Cao
De-Spinning Mechanism: The objective was to develop a lightweight de-spinning mechanism that would mount on an Aeroseed to de-spin and point a payload for tracking purposes. The de-spinning mechanism utilizes two motors stabilizing a payload to enable an Aeroseed drone to track an object within its all-rotating reference frame. The system consists of a test stand motor, payload motor, and other electrical components for controlling the motors.
Team Members: Anthony Camarillo, Shannon Chen, Emily Coleman, Ehab Elrashidy
Sponsored by: The Aerospace Corp.
SAE Baja Gearbox: The objective was to build a compact, lightweight gearbox for the SAE club that can achieve a maximum RPM between 35-37.5 mph, while maintaining the desired torque for desired gradeability. Several years ago the CSULB Society of Automotive Engineers (SAE) Baja team designed their own gearbox that was functional and reliable, but not competitive. We improved upon the previous design through weight reduction, optimization of the gear ratio, and produced a more aggressive acceleration.
Team Members: Dylan Crowley, Michael Vu, Alex Patterson, Derrick Lee, Glenn Piao
Heat Exchanger for Karl Strauss Brewing: Improving the cold water heat exchanger decreased the time it cools water, and increased efficiency of the brewery cooling system. The brite, fermentation, and water tanks are cooled with the same chiller. Therefore, having a more efficient heat exchanger at the cold water system helped. We worked to receive recommendations for heat exchangers to provide to Karl Strauss. We also built a prototype of the cold water heat exchanger.
Team Members: Clayton Congdon, Zach Stasaitis, Ashley Kniss, Jeremy Lan, Jennifer Guess
Industry Supporter: Karl Strauss Brewing Co.
Automated Lubrication System: The auto-lubrication system was created for Performance Forge to automate their lubrication process of aluminum stock and recirculate lubricant back into the system. To achieve this, the system uses a laser sensor that detects an object sending a signal to the microcontroller. The microcontroller turns on the relay sending power to the gear pump, which sprays the aluminum stock. The unused oil drips into a filtered tray pan acting as a reservoir, becoming reusable for the next stock material.
Team Members: Vanna Pheap, Daniel Puentes, Kevin Dang
Industry Supporter: Performance Forge
Strain Detection using Fiber Optic Inside a Conduit: SoCal Gas uses fiber optics sensors to conduct structural health monitoring of gas pipelines. The objective was to design a methodology to monitor strains using fiber optic cable inside a conduit. Encasing the fiber optic cable inside a conduit protects it from hazardous environment which improves its reliability and lifespan. Our design allows the fiber optic cable to be suspended inside a conduit to monitor strain and environmental temperature enabling structural health monitoring of gas pipelines.
Team Members: Emmanuel Diaz, Ernesto Rivera, Fabiola Portillo, Roger D. Contreras
Sponsored by: Southern California Gas Co.
Rotating Mass Wave Energy Converter: This wave energy converter utilizes the oscillating motion of the ocean to rotate an eccentric mass within a buoy. We devised an innovative mechanism by adapting an epicyclic gear arrangement to convert the back and forth oscillating motion of our buoy into a single directional rotary motion. With wave energy being one of the most underutilized forms of renewable energy, we hope to create a more efficient, streamlined design to help grow this industry.
Team Members: Allan Nguyen, Harvey Vazquez, Mauricio Garcia, Michael Herrera, Scott Crane